Reorganisation der Materialplanung bei internationalem Anlagenbauer
Wertstromaufnahme | Frühwarnsystem | Produktions-Forecast
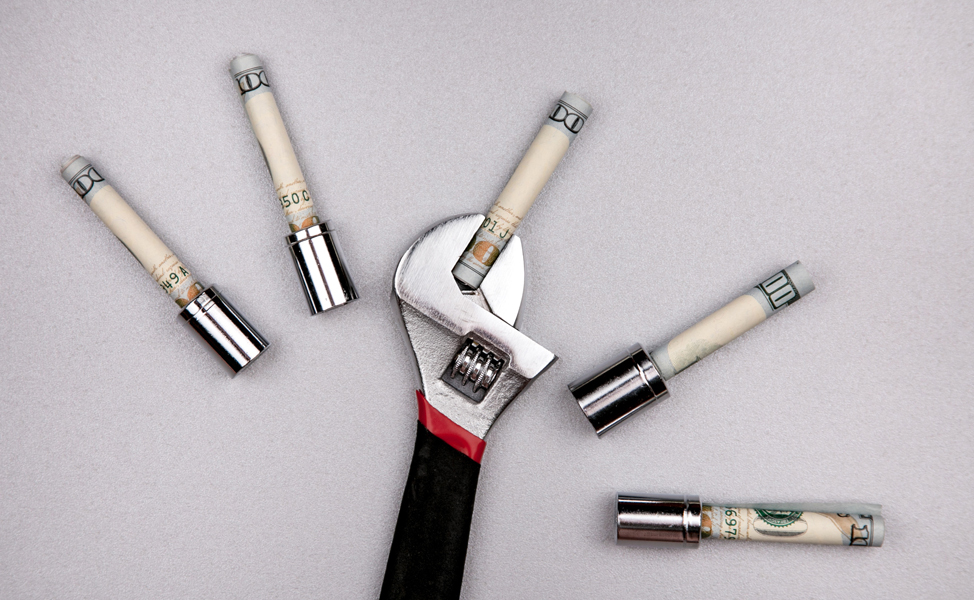
Das Projekt in Stichworten
- Wertstromaufnahme offenbart zahlreiche Mängel im Supply Chain Management
- Neuordnung der Teams und Verantwortlichkeiten in der Materialplanung
- Forecast-Analyse erleichtert rechtzeitige Beschaffung von Komponenten
- Abhängigkeit von kritischen Lieferanten aus Asien durch lokalen Einkauf reduziert
- Frühwarnsystem für Produktionsengpässe entwickelt und Eskalationsregeln festgelegt
- Materialplanung innerhalb von acht Monaten erfolgreich neu aufgestellt
Bei einem international führenden Unternehmen des Anlagenbaus hatten sich über Jahre erhebliche Defizite im Supply Chain Management angesammelt, die sich wegen der durch die Corona-Pandemie verursachten Lieferkettenstörungen noch weiter verschärften. Der heutige Interim Manager wurde in der Schweizer Supply Chain Organisation für Europa als Material Planning Manager engagiert, um die Defizite auszuräumen und mit einer verlässlichen Planung der Materialflüsse für Planungssicherheit in Produktion und Auslieferung zu sorgen.
Als der Materialplanungs-Experte die Aufgabe übernahm, offenbarte sich die ganze Tragweite der Probleme. In der jüngeren Vergangenheit war es wiederholt zu Produktionstopps und kurzfristigen Verschiebungen gekommen. Die verspätete Bearbeitung hatte zu einer erheblichen Verstimmung bei wichtigen Kunden geführt und das Vertrauen der Produktionsleitungen in das Supply Chain Management erheblich gestört. Ein stetig wachsendes Backlog, steigende Kosten durch Überstunden in der Produktion und Umsatzverluste durch nicht erledigte Aufträge drückten die Stimmung im Unternehmen.
Wertstromaufnahme offenbart zahlreiche Mängel im Supply Chain Management
Nach ausführlichen Workshops mit dem Management-Team, Führungskräften aus Produktion und Einkauf sowie den Mitarbeitenden im Bereich Supply Chain analysierte der Experte die Prozesse in der Materialplanung mithilfe einer Wertstromaufnahme (Value Stream Mapping). Dabei stellten sich zwei wesentliche Schwächen heraus: Zum einen verfügte die Materialplanung kaum über belastbare Kennziffern. Zum anderen waren die Verantwortlichkeiten im Supply Chain Management nicht eindeutig geklärt.
Neuordnung der Teams und Verantwortlichkeiten in der Materialplanung
In einigen Bereichen des Supply Chain Managements hatten die unklaren Verantwortlichkeiten dazu geführt, dass wichtige Entscheidungen mitunter erst spät oder gar nicht getroffen wurden. Um diesen Mangel abzustellen, stellte der Interim Manager die entsprechenden Teams neu auf und benannte eindeutige Verantwortlichkeiten. Das beschleunigte notwendige Entscheidungen. Gleichzeitig verbesserte sich die interne Kommunikation, da die Beteiligten für Entscheidungen auf verlässliche Informationen aus unterschiedlichsten Bereichen angewiesen waren – und diese auch einforderten. Mit der Neuverteilung der Zuständigkeiten sorgte der Interim Manager gleichzeitig dafür, dass Doppelarbeiten zukünftig vermieden wurden. Dadurch stieg die Effizienz deutlich.
Forecast-Analyse erleichtert rechtzeitige Beschaffung von Komponenten
Im nächsten Schritt organisierte der Interim Manager ein bereichsübergreifendes Projekt, um alle wichtigen Produktions- und Lieferdaten zusammenzufassen und eine Vorhersage für die Bedarfe in der Produktion abzuleiten. Dabei identifizierte er in enger Abstimmung mit Einkauf, Sales und Marketing beispielsweise, welche Komponenten besonders häufig verwendet werden oder lange Lieferfristen haben – und daher in höherer Anzahl vorgehalten werden sollten, um eine schnelle Verfügbarkeit zu garantieren. Aus dieser Analyse leitete der Interim Manager mit dem Einkauf entsprechend frühzeitige Liefertermine für Lieferanten ab.
Abhängigkeit von kritischen Lieferanten aus Asien durch lokalen Einkauf reduziert
Im Zuge dieser Forecast-Analyse stellte der Interim Manager ferner fest, dass das Unternehmen zahlreiche Komponenten von Lieferanten aus Asien bezog. Für viele dieser Lieferanten gab es keine Fallback-Lösung, also keine zweite Bezugsquelle. Um angesichts der Erfahrung aus der Corona-Pandemie (oder anderer Krisen wie der Ukraine-Krieg) das entsprechend hohe Ausfallrisiko zu minimieren, überzeugte er die Geschäftsführung davon, trotz höherer Preise alternativ lokale Lieferanten zu finden. Denn die Gesamtkosten (TOC: Total Cost of Ownership) fallen trotz der höheren Kosten geringer aus, wenn Produktionstops verhindert werden können.
Frühwarnsystem für Produktionsengpässe entwickelt und Eskalationsregeln festgelegt
Um möglichst frühzeitig auf Lieferkettenprobleme reagieren zu können, leitete der Interim Manager aus dem Datenbestand ein Frühwarnsystem ab, das in einem Dashboard den aktuellen Status aufzeigt. Für kritische Entwicklungen definierte er Eskalationsregeln, die sicherstellen, dass Produktion und Auslieferung solcher Kundenaufträge früh vorrangig bearbeitet werden können.
Materialplanung innerhalb von acht Monaten erfolgreich neu aufgestellt
Nach acht Monaten hatte der Interim Manager die Materialplanung erfolgreich neu aufgestellt. Das Unternehmen verfügt nunmehr über eine zuverlässige Materialplanung und darüber hinaus über ein Frühwarnsystem, dass sich abzeichnende Probleme früh aufzeigt – und schnelle Reaktionen ermöglicht. Die klaren Zuständigkeiten im Supply Chain Team haben dafür gesorgt, dass Entscheidungen rechtzeitig und effizient getroffen werden.
Nach Optimierung der Materialplanung und der nachgelagerten Prozesse läuft die Produktion ohne ungeplante Stopps oder Umstellungen. Liefertreue und Kundenzufriedenheit haben sich deutlich verbessert. Das bereichsübergreifende Vertrauen ist wieder hergestellt – und die Motivation der Beschäftigten deutlich gestiegen.
Buchen Sie jetzt online einen Gesprächstermin mit einem Consultant Ihrer Wahl.
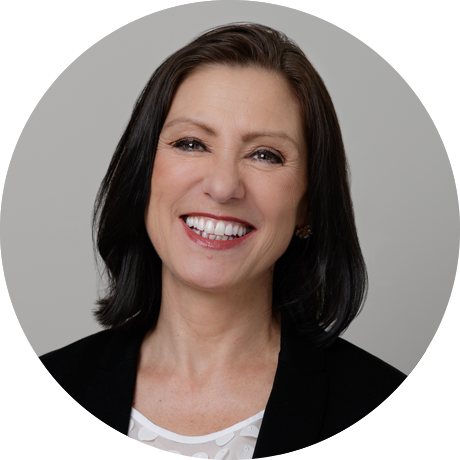
Claudia M. Christen
Senior Consultant
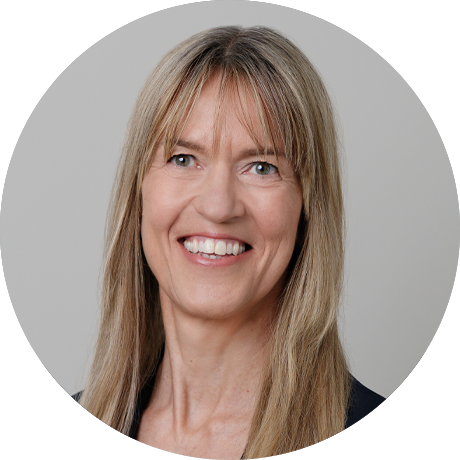