Qualitätssicherung: Troubleshooting bei Automotive-Zulieferer (KMU)
Werksaudit – Grenzmuster-Meeting – Fehlersuche

Das Projekt im Überblick:
- OEM stellt Zulieferer unter Kontrolle und sperrt Neuvergaben
- Intensive Fehlersuche vor Ort – Grenzmuster-Meeting mit dem OEM
- Verbleibende kleinere Qualitätsmängel identifiziert und abgestellt
- OEM gibt Produktion und Neuvergabe nach erfolgreichem Werksaudit frei
- Projekt in der Hälfte der geplanten Zeit beendet (4 Wochen)
Der Interim Manager wurde von einem inhabergeführten Automobilzulieferer als Troubleshooter engagiert. Der TIER 1 und TIER 2 Zulieferer mit Hauptsitz in Deutschland und 2 Werken in Europa liefert unter anderem werktäglich ca. 8.000 identische Innenraumteile (Kunststoffspritzguss) an einen 300 km entfernten Hersteller (OEM).
OEM stellt Zulieferer unter Kontrolle und sperrt Neuvergaben
Der OEM hatte bei der Qualitätskontrolle in seinem Werk mehrere dieser Innenraumteile mit Oberflächenbeschädigungen gefunden. Daraufhin verpflichtete der OEM den Zulieferer, alle Teilebestände und alle weiteren Lieferungen auf eigene Kosten von einer externen Sortierfirma seiner Wahl kontrollieren zu lassen (Q-Wall). Dadurch entstanden dem Zulieferer monatliche Zusatzkosten von weit über 50.000 Euro.
Trotz intensiver Bemühungen des Zulieferers zur Qualitätssicherung fand die Sortierfirma auch nach mehreren Wochen noch Teile mit Oberflächenfehlern. Der OEM bestand in der Folge darauf, alle 8.000 Teile täglich weiterhin manuell kontrollieren zu lassen. Zusätzlich sperrte der OEM den Zulieferer für die Vergabe von Neugeschäft.
Intensive Fehlersuche vor Ort – Grenzmuster-Meeting mit dem OEM
Der Interim Manager agierte in dem Mandat als Troubleshooter und Supply Chain Berater im Produktionswerk. Nach ausführlichen Besprechungen mit dem Inhaber, dem Werkleiter, dem Abteilungsleiter QS und Mitarbeitern aus der Produktion machte er sich selbst ein Bild von allen Arbeitsplätzen. Er besuchte auch die 300 km entfernte externe Sortierfirma und begleitete diese ganztägig. Dabei ließ er sich jedes Teil zeigen, das als schlecht identifiziert wurde.
Nach wenigen Tagen stellte sich heraus, dass die Mitarbeiter der Sortierfirma in ihrem Bemühen um bestmögliche Arbeit Teile aussortierten, die aus Sicht des Interim Managers den Anforderungen des OEM vollauf genügen. Daraufhin initiierte und organisierte er ein Grenzmuster-Meeting mit einem Mitarbeiter der Qualitätssicherung des OEM-Kunden. Dieses Treffen gab den Beteiligten mehr Sicherheit und Klarheit darüber, welche Teile vom OEM akzeptiert und welche abgelehnt werden.
Verbleibende kleinere Qualitätsmängel identifiziert und abgestellt
Nach dieser Abstimmung verblieb ein kleiner Rest an Nicht-in-Ordnung-Teilen (NIO-Teilen). In enger Zusammenarbeit mit dem Abteilungsleiter Qualität des Zulieferers konnten kleine Schwächen identifiziert und abgestellt werden. Zu den Maßnahmen zählt eine tägliche ABC-Analyse. Sie hilft allen Beteiligten, sich aufs Wesentliche zu konzentrieren. Nach weiteren 14 Tagen fand die Sortierfirma keine schlechten Teile mehr.
OEM gibt Produktion und Neuvergabe nach erfolgreichem Werksaudit frei
Der OEM würdigte das Ergebnis und kündigte an, den Zulieferer zu auditieren, um final entscheiden zu können, ob die Sortierfirma ihre Arbeit einstellen darf. Das Audit bereitete der Interim Manager gemeinsam mit Führungskräften und Mitarbeitern im Werk vor und begleitet es auch.
Das Werksaudit wurde erfolgreich bestanden. Der OEM-Kunde hat die externe Sortierfirma gestoppt und den Zulieferer wieder für die Vergabe von Neugeschäft freigegeben.
Zum Ergebnis des Beratungsprojektes zählt auch, dass mehrere Arbeitsanweisungen und Einarbeitungspläne der Produktionsmitarbeiter angepasst wurden. Zu den Erfolgen dieses Troubleshooting-Projektes zählt ferner, dass die Ziele in 4 statt der geplanten 8 Wochen erreicht wurden.
Buchen Sie jetzt online einen Gesprächstermin mit einem Consultant Ihrer Wahl.
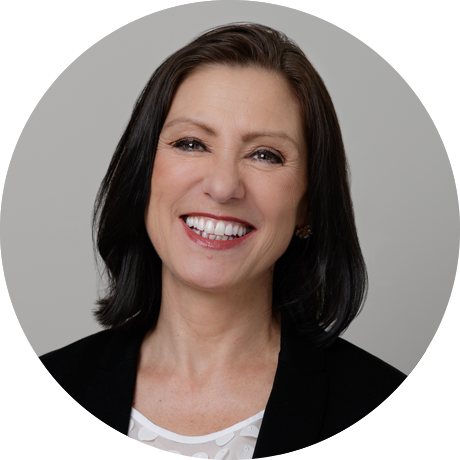
Claudia M. Christen
Senior Consultant
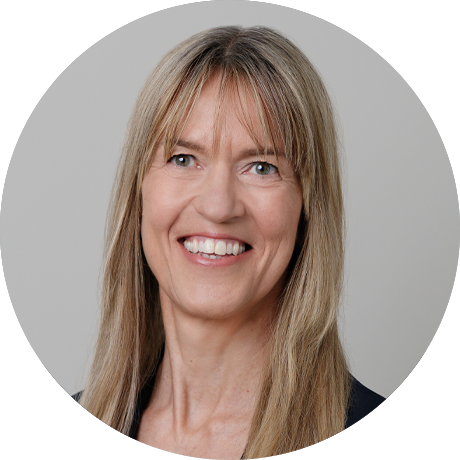